Just a few pics of what I'm having built for us. It will eventually encompass 350' of 1 3/4 x .120 4130, so needless to say it will be a heavy bitch! We're doing this primarily in the interest of safety, and to make a few changes to our current frame. We dune with a couple of very nice cars, a fresh Ricochet, a new Tatum TRX4 and a 2 seater that's getting a makeover as we speak... so we felt the need to upgrade as well. There is a lot more done than what I am posting photos of but I will wait until it is further along before I reveal exactly what our fabricator has built for us.
Did I mention that this will be strong? This front bulkhead assembly is .250 4130, the upper tubes that support the shock bridges are .188 4130, all tig welded of course. The rest of the frame is rooted and capped like a trophy truck chassis, the .120 wall thickness allows a very hot root pass to burn the puddle in good. Again this is NOT my handywork. I'll post more pics in this thread in the future. Sorry to sound like this is the greatest sand car frame ever but it's been building for a good while now and few have actually seen it, so the excitement has not been shared with anyone yet. In future installments I'll post some photos of my buddies brand new 800A Miller Dynasty :bow1: Enjoy these for now.
It's kicked up 10* with a fixture jig on purpose so it can be attached to the fixture table.
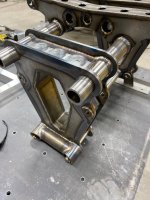
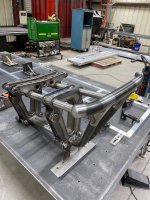
The bottom tubes are just the root pass while the top has the cap. I'm not at liberty to say what filler rod was used, there was much discussion about it. I can say that the 10lbs that I bought was not cheap LOL. We were originally going to send the modular front bulkhead out for heat treatment to toughen it up but ultimately we were unable to do so because the filler rod will not accept normalization. Due to the wall thickness of the materials we chose we accepted the tradeoff.

Did I mention that this will be strong? This front bulkhead assembly is .250 4130, the upper tubes that support the shock bridges are .188 4130, all tig welded of course. The rest of the frame is rooted and capped like a trophy truck chassis, the .120 wall thickness allows a very hot root pass to burn the puddle in good. Again this is NOT my handywork. I'll post more pics in this thread in the future. Sorry to sound like this is the greatest sand car frame ever but it's been building for a good while now and few have actually seen it, so the excitement has not been shared with anyone yet. In future installments I'll post some photos of my buddies brand new 800A Miller Dynasty :bow1: Enjoy these for now.
It's kicked up 10* with a fixture jig on purpose so it can be attached to the fixture table.
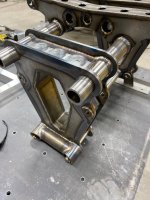
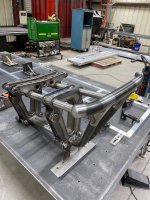
The bottom tubes are just the root pass while the top has the cap. I'm not at liberty to say what filler rod was used, there was much discussion about it. I can say that the 10lbs that I bought was not cheap LOL. We were originally going to send the modular front bulkhead out for heat treatment to toughen it up but ultimately we were unable to do so because the filler rod will not accept normalization. Due to the wall thickness of the materials we chose we accepted the tradeoff.

Last edited by a moderator: