Dune-Track-N
Well-known member
- May 5, 2021
- 1,075
- 932
Rebuilding this thread boats almost water ready....... I'll try to recap some of the major items.
Back story... we had a 77' Charger MiniDay cruiser that went 55-60mph but we'd lost 3 engines in it and my wife wanted to go FASTER. So I told her to find the boat she liked and she fell in love with the Sanger SuperJets.
She's named this "Pixey Dust"
I picked this up late summer 2019 and just started the tear down for rebuild by April 2020 (now 2021.... a year late). Here's the progress and updates daily/weekly/monthly/yearly. It's had different motors and interior, when I got it there was an Olds 455 and junk interior (was told it had a BIG chevy at one time but the mounts didn't show that). Old's had two dead holes and my BBC had just spun the bottom end, so pulled and sold the OLDs rebuilding the BBC.
Day1 buy the boat and do one lake test, boat ran ok. Got up to 45mph but nothing really worked and the seats were horrible. We new the floor had rot in it when we bought it, so we planned to fix that.
Day2 compression test and pulling the Olds (came with extra over transom exhaust)
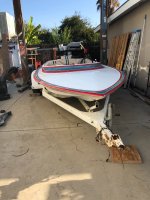
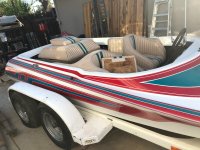
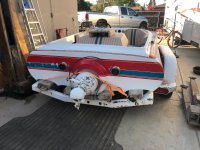
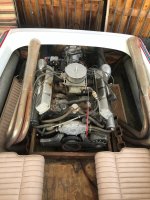
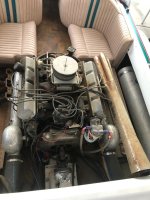
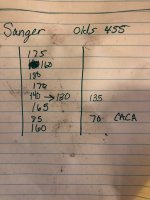
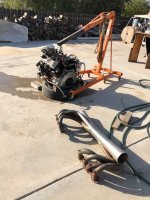
Back story... we had a 77' Charger MiniDay cruiser that went 55-60mph but we'd lost 3 engines in it and my wife wanted to go FASTER. So I told her to find the boat she liked and she fell in love with the Sanger SuperJets.
She's named this "Pixey Dust"
I picked this up late summer 2019 and just started the tear down for rebuild by April 2020 (now 2021.... a year late). Here's the progress and updates daily/weekly/monthly/yearly. It's had different motors and interior, when I got it there was an Olds 455 and junk interior (was told it had a BIG chevy at one time but the mounts didn't show that). Old's had two dead holes and my BBC had just spun the bottom end, so pulled and sold the OLDs rebuilding the BBC.
Day1 buy the boat and do one lake test, boat ran ok. Got up to 45mph but nothing really worked and the seats were horrible. We new the floor had rot in it when we bought it, so we planned to fix that.
Day2 compression test and pulling the Olds (came with extra over transom exhaust)
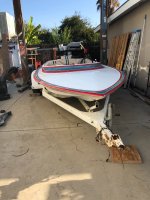
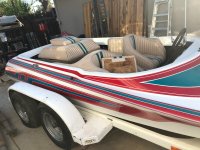
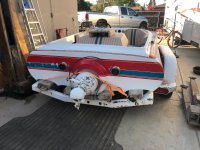
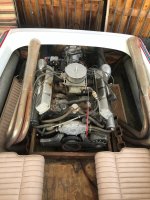
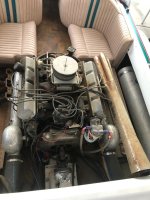
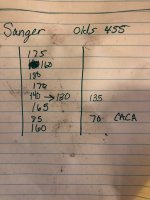
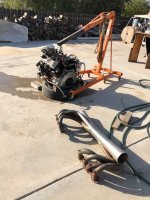