Richard h
Well-known member
- May 5, 2021
- 1,462
- 1,323
So when I finally decided to make the change from a type one (Autocraft) transaxle to a Mendi 2d one of the hurdles was building new trailing arms. The larger ring gear sets your axle center line back on a mid engine. I wanted to keep the same rear width so I made a jig with the old arms, cut apart and simply slid the rear bearing housing back the distance I wanted for the new arms. I used 1.25" 120 tubing. After I got done and painted and on the car, they looked to small and weak at the front joints. I removed them again and cut the front tubing off and sleeved it with 1.5" .120 and put 7/8" hiem joints on them. Second paint I just used steel it. They work great and glad I never tried the first ones as I had no confidence in them.
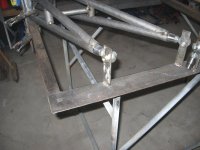
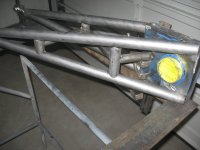

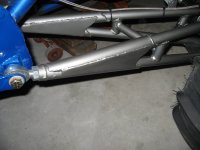
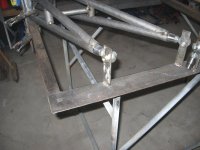
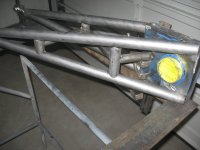

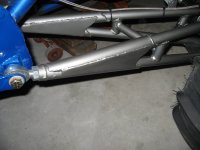