SeanRitchie
Well-known member
- May 6, 2021
- 404
- 959
A common question. What is the difference between sequential and synchromesh (or H-pattern) shifting gearboxes?
I will almost always recommend a synchronized gearbox to the recreational user, or to anyone that plans on having multiple people drive their car. Synchronized H-pattern gearboxes are somewhat fool-proof and operate like any manual shift transmission in a common production car. They are difficult to damage when used properly and will often outlast sequential shifting components.
Sequential gearboxes require some knowledge and coordination between throttle input and shifter operation to shift properly without causing damage to the gears. They are great for performance applications and are often times the strongest option available for high powered applications. They offer the fastest shifting, can be operated with no-lift-shift electronics packages, and can even be operated via paddle shifters.
The basics: Synchromesh gearboxes will typically be an H-pattern type shift arrangement (but there are sequential type shifters that can be used with synchronized gearboxes). Synchronized gears utilize a system of small engagement teeth on the selector sleeve (or slider) that is forced into each gear with the shift fork. The gear itself has a matching set of teeth that engage the slider teeth, which is what connects the gear to the output shaft through the slider/hub assembly and completes the gear ratio.
To aid in engagement of these small teeth, a small ring called a synchronizer is placed between the slider and gear. This synchro is commonly made of brass, but can be made of other materials. This synchronizer sits on a cone machined onto the gear. The cone shape allows the synchro to float and spin free when not being used, as the synchro is spinning at the same speed as the output shaft with the gear that currently selected.
During the shift, the synchronizer is forced onto the cone of the gear as the slider moves towards the gear being selected. The synchronizer will either speed up or slow down the speed of the gear as it is forced onto the cone of the gear. Once these speeds have been matched, the slider teeth can then slip over the synchro and engage the teeth of the gear to complete the connection of the gear to the output shaft.
This style of gearbox is easy to operate as the synchronizers change the speed of the gear before the gear can be engaged in a smooth and easy operation. The downside to this style of mechanism is that the synchros take time to change the speed of the gears, and therefore is a slower shift actuation before the clutch can be released and power can be driven through the gearbox again.
Synchros will wear with use, and will eventually wear to the point where the synchro sits low on the cone of the gear. This is when the gears will grind as you engage the gear. Synchros can also break into pieces if forced too hard against the gear. A synchro gearbox should be shifted slow and smooth to allow the synchro to change the speed of the gear for an easy engagement.
Another common complaint with synchronized gearboxes is hard shifting in cold weather. This is often due to thick oil being used to help protect the gears and high powered engines. The cold, thick oil is packed in between the synchro and cone surface of the gear. As the synchro is pushed onto the gear, the cold oil does not get out of the way and the synchro slips on the cone of the gear rather than grab and change the speed of the gear. This will often get better as the gear oil warms and thins out. Another similar symptom is caused by oils that are too slippery, and not allowing the synchro to have enough friction with the gear to slow it down or speed it up to complete the shift.
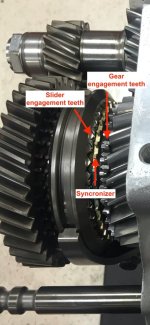
I will almost always recommend a synchronized gearbox to the recreational user, or to anyone that plans on having multiple people drive their car. Synchronized H-pattern gearboxes are somewhat fool-proof and operate like any manual shift transmission in a common production car. They are difficult to damage when used properly and will often outlast sequential shifting components.
Sequential gearboxes require some knowledge and coordination between throttle input and shifter operation to shift properly without causing damage to the gears. They are great for performance applications and are often times the strongest option available for high powered applications. They offer the fastest shifting, can be operated with no-lift-shift electronics packages, and can even be operated via paddle shifters.
The basics: Synchromesh gearboxes will typically be an H-pattern type shift arrangement (but there are sequential type shifters that can be used with synchronized gearboxes). Synchronized gears utilize a system of small engagement teeth on the selector sleeve (or slider) that is forced into each gear with the shift fork. The gear itself has a matching set of teeth that engage the slider teeth, which is what connects the gear to the output shaft through the slider/hub assembly and completes the gear ratio.
To aid in engagement of these small teeth, a small ring called a synchronizer is placed between the slider and gear. This synchro is commonly made of brass, but can be made of other materials. This synchronizer sits on a cone machined onto the gear. The cone shape allows the synchro to float and spin free when not being used, as the synchro is spinning at the same speed as the output shaft with the gear that currently selected.
During the shift, the synchronizer is forced onto the cone of the gear as the slider moves towards the gear being selected. The synchronizer will either speed up or slow down the speed of the gear as it is forced onto the cone of the gear. Once these speeds have been matched, the slider teeth can then slip over the synchro and engage the teeth of the gear to complete the connection of the gear to the output shaft.
This style of gearbox is easy to operate as the synchronizers change the speed of the gear before the gear can be engaged in a smooth and easy operation. The downside to this style of mechanism is that the synchros take time to change the speed of the gears, and therefore is a slower shift actuation before the clutch can be released and power can be driven through the gearbox again.
Synchros will wear with use, and will eventually wear to the point where the synchro sits low on the cone of the gear. This is when the gears will grind as you engage the gear. Synchros can also break into pieces if forced too hard against the gear. A synchro gearbox should be shifted slow and smooth to allow the synchro to change the speed of the gear for an easy engagement.
Another common complaint with synchronized gearboxes is hard shifting in cold weather. This is often due to thick oil being used to help protect the gears and high powered engines. The cold, thick oil is packed in between the synchro and cone surface of the gear. As the synchro is pushed onto the gear, the cold oil does not get out of the way and the synchro slips on the cone of the gear rather than grab and change the speed of the gear. This will often get better as the gear oil warms and thins out. Another similar symptom is caused by oils that are too slippery, and not allowing the synchro to have enough friction with the gear to slow it down or speed it up to complete the shift.
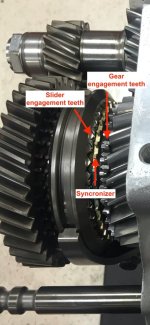