Richard h
Well-known member
- May 5, 2021
- 1,462
- 1,323
So, I got this to repair today. YIKES! Lots of dead tubes. Hopefully it will be a little better when I'm done. Did some serious looking and discussion and think a plan came together. Going to require some panel modification though as more tubes are to be added.
Like doing this stuff and it is for a friend, so I don't charge for anything except materials.
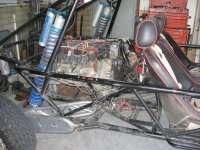
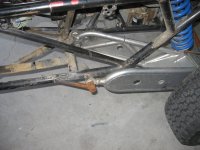
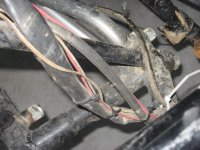
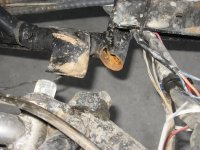
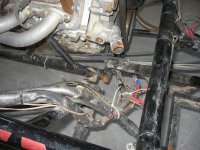
Like doing this stuff and it is for a friend, so I don't charge for anything except materials.
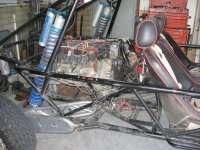
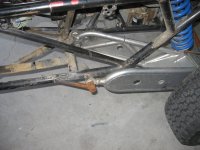
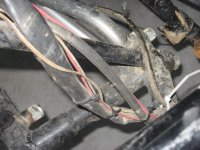
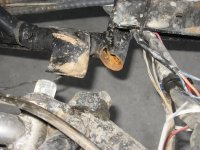
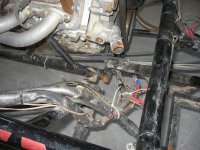