Jammer75
Well-known member
- May 5, 2021
- 542
- 493
Current set up
4 seater 2.0 Subaru
Fox 2.5 Coil over Remote Reservoir
16" stroke (only using 10.5" of stroke) 7/8" shaft
springs were checked and are as follows
Bottom spring 16" 363lbs
Top Spring 14" 288lbs
1" preload
150psi in reservoirs
After gradually going up on the comp/rebound this is where i ended up and still bottom out and kick
Comp valving #95 Rebound Valving #85
1.8 2x0.010 1.6 0.012
0.095 0.01 (flutter) 1.425 0.015
1.6 2x0.010 1.35 0.015
1.425 0.015 1.1 0.015
1.35 0.015 .095 0.015
1.1 0.015 0.8 0.015
0.95 0.015 Back up .750 0.2
0.8 0.02
Top Out 1.570 0.128
What I know
Fox 2.5 Coil over Remote Reservoir 16" 7/8" shaft
corner weight is 758lbs
distance from swingarm pivot bolt to wheel center bolt is 25"
distance from swingarm pivot bolt to lower shock mount is 21"
amount of shock shaft showing at full droop is 10.5-11"
shock angle is 20 degrees
rear sand tire weighs 47lbs
I feel this thing is under sprung-
not sure what would be the best and what is a good amount of droop%
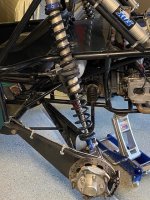
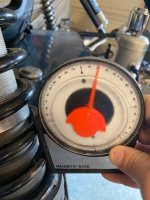
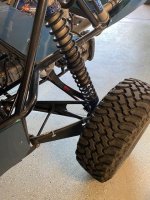
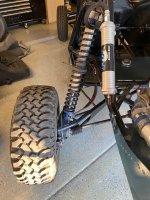
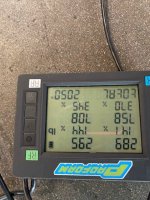

4 seater 2.0 Subaru
Fox 2.5 Coil over Remote Reservoir
16" stroke (only using 10.5" of stroke) 7/8" shaft
springs were checked and are as follows
Bottom spring 16" 363lbs
Top Spring 14" 288lbs
1" preload
150psi in reservoirs
After gradually going up on the comp/rebound this is where i ended up and still bottom out and kick
Comp valving #95 Rebound Valving #85
1.8 2x0.010 1.6 0.012
0.095 0.01 (flutter) 1.425 0.015
1.6 2x0.010 1.35 0.015
1.425 0.015 1.1 0.015
1.35 0.015 .095 0.015
1.1 0.015 0.8 0.015
0.95 0.015 Back up .750 0.2
0.8 0.02
Top Out 1.570 0.128
What I know
Fox 2.5 Coil over Remote Reservoir 16" 7/8" shaft
corner weight is 758lbs
distance from swingarm pivot bolt to wheel center bolt is 25"
distance from swingarm pivot bolt to lower shock mount is 21"
amount of shock shaft showing at full droop is 10.5-11"
shock angle is 20 degrees
rear sand tire weighs 47lbs
I feel this thing is under sprung-
not sure what would be the best and what is a good amount of droop%
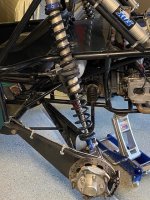
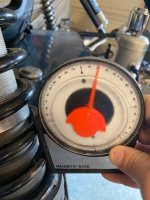
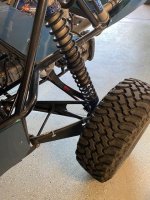
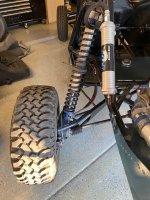
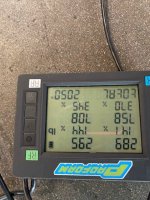

Last edited by a moderator: