MPC
Member
- Jan 18, 2023
- 98
- 76
I am converting my buggy from combo spindles to 2" hollow spindles with disc brakes. The race on the inboard side of the hub gets hung up on a slight lip; the lip the pencil is pointing to in the picture. I assume the race and bearing should be going all the way down to the bottom to fully seat. If so, what would be the preferred method to get it all the way into position?
I have been putting the race in the freezer (15 minutes or so) and that hasn't got it past the small lip. Maybe I just need to leave it in overnight??
I'm hesitant to beat it into place and damage the race. Should I deburr it with a rotary tool/sand paper?
Both hubs have the same small lip. Thanks
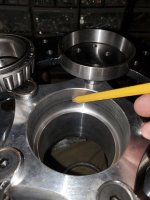
I have been putting the race in the freezer (15 minutes or so) and that hasn't got it past the small lip. Maybe I just need to leave it in overnight??
I'm hesitant to beat it into place and damage the race. Should I deburr it with a rotary tool/sand paper?
Both hubs have the same small lip. Thanks
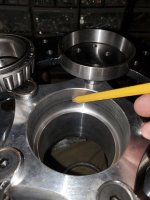